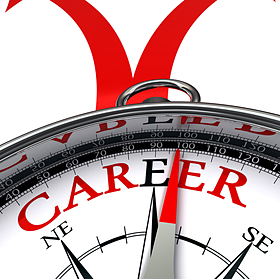
Industrial Engineer ► Quality Manager ► Expert in Quality Assurance and Continuous Improvement ► FMEA Developer
Javier Garcia - Verdugo Sanchez's Bio:
Javier Garcia - Verdugo Sanchez's Experience:
-
Currently exploring new opportunities all over the world at Preferable Automotive Industry
February 2015 - Present | - WorldwideI am open and ready to relocate or travel any time and anywhere in the world for the organization purposes and interests, in order to become an integral part of the company.
-
Quality Management System Responsible and Information Technology Developer at B. A. M. G. y Asociados, S. L.
August 2012 - February 2015 | Madrid► Successful development and implementation of the Quality Management System according to the ISO 9001:2008 standard. ► Establishment of a practical framework for Strategic Quality Management in the company by applying the Quality Function Deployment (QFD) principles. ► Optimal development and implementation of the Business Process Management (BPM) principles and practices. ► Continuous Improvement of the methods and techniques for all operations of the company through the implementation of Quality Tools. ► Effective definition, design and implementation of the Documental Management System. ► Development, coaching and training of the personnel in order to improve the effectiveness and efficiency of the Internal Processes.
-
Quality Management Systems Coordinator and Quality Continuous Improvement Responsible at Knorr-Bremse Spain
2008 - 2012►Implementation of the International Railway Industry Standard (IRIS) and successful certification of the Quality Management System according to this Standard. ►Active collaboration in the development of an Integrated Management System (Quality, Enviroment, Health and Safety) based in the Business Process Management (BPM) principles. Process Modelling using the ARIS software platform. ►Design and Implementation of a new Documental Management System. ►Effective implementation, management and performance of the internal Audits Schedule for the Quality Management System and Manufacturing Processes. Management and follow up of the Corrective Action Plans. ►Excellent driving and follow up of the Continuous Improvement Program and key contributor for the verification of the effectiveness of the Improvements and Preventive activities. ►Practical implementation of Quality Tools such as: Root Cause Analysis, Eight Disciplines (8D), Plan – Do – Check – Act Cycle (PDCA), 5 Whys, Design and Process FMEA, Poka Yoke, Statistical Process Control (SPC), etc. ► Definition and implementation of Quality self-control checks executed by the operators on the production lines. ►Effective coaching, training, and development of the Quality Team members and other plant personnel in Quality Management System principles and Quality Tools. ► Development of Process FMEA and Design FMEA leading cross-functional teams. Leader role at a international team responsible for the development of the Design FMEA for the Modular HVAC equipment of Merak Sistemas Integrados de Climatizacion. ► In charge of the Special Processes of bonding, crimping, riveting and brazing.
-
Quality Manager at Nagamohr, S. A.
1997 - December 2007► Implementation and certification of the Quality Management System ( QMS ) according to the ISO 9002:1994 Standard requirements. ► Implementation of Valeo 1000 Standard within the QMS. ► Implementation of ISO/TS 16949:2002 Standard requirements and certification, ► Establishment of an effective process for the Documental Control and Management. ► Development and implementation of Process Quality Control Plans. ► Definition and implementation of Quality Self-Control checks executed by the operators on the production lines. ► Practical implementation of Quality Tools: Root Cause Analysis, FTA, 8D, PDCA, 5 Whys, QRQC, Process FMEA, Design Of Experiments, Poka Yoke, SPC, Machine and Process Capability ( Cp, Cpk, Pp, Ppk ), Fishbone Diagram, Pareto, Flow Charts, Risk Management, ANOVA, etc. ► Training, coaching and qualification of manufacturing personnel on Quality Tools and Quality Management System ( QMS ) basic concepts. ► Implementation of APQP (Advanced Product Quality Planning) process and activities. ► Management of the PPAP Process (Production Part Approval Process). ► Planification and Assurance of the Quality level within the Supply Chain. ► Management of the calibration program for all measurement instruments and equipments. ► Planning and performance of Measurement System Analysis ( MSA ). ► Implementation, management and conducting of the internal Audits Schedule for the Quality Management System ( QMS ), manufacturing processes and product audits. Management and follow up of Corrective Action Plans. ► Definition, tracking and analysis of Key Performance Indicators (KPI ). ► Development and follow up of a Yearly Program for Quality Improvements in order to reach the excelence in Quality Continuous Improvement. ► Development, update and maintenance of Process Failure Mode and Effects Analysis ( FMEA ). ► Development and Management of the Company's Health & Safety Program.
-
Quality Engineer at Trefiladora Madrilena, S. A.
March 1996 - December 1996► Support on the Design, Development and Implementation of a Quality Management System ( QMS ) in order to meet the requirements of the ISO 9001:1994 Standard. ► Creation, update and maintenance of the Quality Manual, Operational Procedures, Work Instructions, record formats and templates and other documentation from the Quality Management System ( QMS ). ► Documental Control and Management. ► Planning and review of the yearly Internal and External Audits Program. ► Role of Internal Quality Auditor, conducting products, manufacturing processes and Quality Management System ( QMS ) Audits. ► Coordination of external and Customer Audits and participation in them. ► Assistance and support to the Quality Management System Responsible in reference to the diverse Quality Management System tasks, e.g.: Change Controls, Quality Deviations, Quality Incidences, Customer Complaints, Measurement Devices, Supplier Quality Assurance, and so on. ► Coordination, coaching, training and developing of Quality Team members and other plant personnel on basic principles on Quality Assurance and Quality Tools. ► Promotion of Quality Awareness at all levels of the organization. ► Practical implementation of Quality Tools: Brainstorming, Cause and Effect Diagrams ( Ishikawa ), Design of Experiments ( DOE ), Eight Disciplines ( 8D ), Flow Charts, and so on. ► Support in Process Failure Mode and Effects Analysis ( FMEA ) and Control Plans development and implementation. ► Inspection of production operation periodically and check on the proper implementation of Quality Operating Procedures and Control Plans during the production operation.
-
Technical and Quality Assurance Manager at Guijarro Hermanos, S.L. - FAPESA (Fabrica de Aparatos de Proteccion Electrica)
March 1993 - September 1995As Technical Manager: ► Technical leading role on the research and development activities of Miniature Circuit Breakers (MCB) and Earth Leakage Circuit Breakers (ELCB). ► Customer technical advice and support in electrical protection solutions. ► Review of Customer specifications and requirements as well as applicable standards and regulations ( UNE - EN - ISO - BS - DIN ) related to MCB and ELCB inspection / testing protocols, product approval and conformity. ► Methods-Time Measurement ( MTM ) deployment. Manufacturing processes analysis and optimization. Identification and elimination of the manufacturing waste and non-value-added activities. Productivity Improvement. Supplier and Customer Quality activities: ► Development and implementation of the Supplier Quality Assurance ( SQA ) Plan. Quality Assurance of the Incoming Product. ► Outstanding performance on Customer complaints investigation, Problem Solving, Root Cause Analysis and support to aftersales service function. ► Establishment of a system for effectively handling and resolving Customer complaints. ► Defect analysis of Customer return material. Improvements in products / manufacturing processes for reducing Customer rejections and costs of warranty. Manufacturing Processes Quality activities: ► Responsibility for monitoring the Product and Manufacturing Processes Quality. ► Leadership in the management and execution of Improvement Projects across the organization. ► Assurance that the products with the compulsory certification mark were manufactured in conformity with the standards according to which they had been certified. ► Development of training / coaching programs for the Quality Assurance on the company and delivery of training to the manufacturing personnel. ► Promotion of the Quality Awareness among the employees. Quality Management System: ► Effective design and implementation of the Quality Management System of the organization. ► Documental Control and Management.
Javier Garcia - Verdugo Sanchez's Education:
-
Fraunhofer IFAM (Bremen – Germany)
2010 – 2010European Adhesive Specialist (EAS)Concentration: Training validated by the European Federation for Welding, Joining & Cutting (EWF)Activities: ► Ability to prepare work instructions. ► Ability to supervise workers on theoretical and practical matters. ► Ability to plan, to organize and to monitor adhresive processes. ► Ability to monitor process parameters and to adjust them. ► Ability to identify irregularities and to respond accordingly. -
Instituto Madrileno de Formacion
2004 – 2005Master Degree in Prevention of Occupational Risks (Advanced Expert)Concentration: Occupational Safety.Activities: Develop the competencies needed to be effective in the development, implementation, and evaluation of health and safety programs and systems in a wide variety of occupational settings. -
Universidad Politecnica de Madrid
1984 – 1992Upper Degree in Industrial EngineeringConcentration: Metallurgy and Iron and Steel Industry. Average grade of the academic record: notable. -
Additional Training and Coaching
Diplomas on several mattersActivities: ► International Railway Industry Standard (IRIS) Internal Auditor Training Course. ► Finances for non financial people. ► Leadership. ► Communication Strategies. ► Various courses and seminars related with Quality Tools: Metrology, Poka – Yoke, Plan – Do – Check – Act Cycle (PDCA), Factors Tree Análisis (FTA), 8 Disciplines (8D), etc. -
Computer Skills
Activities: ► Working knowledge of PC operating systems (Windows) and hardware installation. ► Proficient on computer software: Microsoft Excel, Word, Power Point, Access, Visio, databases, Autocad, Web Tools, Internet. ► Proficiency in Information Technology Systems used in Quality Management Systems and Business Processes Management: MiniTAB, ARIS software (Business Process Management), IRIS Audit - Tool, and so on. -
Language Skills
Activities: ► Spanish - Mother tonge. ►English - Proficient user in verbal and written communication.
Javier Garcia - Verdugo Sanchez's Interests & Activities:
Piano composition and music production. English learning. Creative fotography. Writing. Reading (technical books and magazines). Quality Assurance, Quality Awareness, Quality Management System, QMS, Quality Strategic Implementation, Business Process Management, BPM, International Railway Industry Standard, IRIS, ISO/TS 16949, ISO 9001, Continuous Improvement, Quality Tools, Statistic Process Control, SPC, Pareto, Eight Disciplines, 8D, Quick Response Quality Control, QRQC, Machine and Process Capability, Cp, Cpk, Pp, Ppk, Design Of Experiments, DOE , Poka Yoke, Production Part Approval Process, PPAP, Avanced Product Quality Planning, APQP, 5S, Visual Management, Problem Solving Tools, Root Cause Analysis, 5 Whys, PDCA, Risk Management, Corrective Actions – Preventive Actions, CAPA, Design and Process Failure Mode and Effects Analysis, FMEA, Supplier Quality Assurance, Process Improvement, Control Plans, Measurement System Analysis, MSA, Quality Management System Audits, Manufacturing Processes Audits, Quality Auditor, KPI.